1980年 - 1990年
経営方針の転換 〜ダイカスト会社との直接取引へ
藤井金型が、資本金500万円の「有限会社 フジイ金型」として法人化されたちょうどそのころ、仕事量が非常に不安定になり、受注が途絶えた。原因は不明である。社長の藤井祥三は榊間と話し合い、経営方針に関わる大きな決断を行なった。プラスチック金型の受注を一切やめ、ダイカスト会社との直接取引に専業することである。
最大の理由は、自社に競争力がないということだ。江南工場敷地をともに間借りしている会社のうち2社は、プラスチック金型を製造していた。また、工場のオーナー自身もプラスチック金型の製造を行なっており、資金力もあった。将来を考えても、これでは競合に打ち勝つことができない。ダイカスト用金型の製造方法のノウハウや設備自体は持っているので、転換は容易である。
あわせて他の金型会社の下請けもやめた。受注のない中で大きなリスクではあったが、他社の下請けをやっている限り、いくら質の良いものを作っても「フジイの金型」としてPRすることはできない。1社の受注に依存せず、複数の会社と取引し納品することを、社の方針として決めた。
さらに業務担当の変更を行なった。社長と営業を兼任していた藤井祥三が製造になり、設計と製造を担当していた榊間が主に外回りをすることにした。20歳になったばかりの榊間の方がフットワークが軽く、新規開拓もしやすい。
この戦略はうまく当たった。当時ダイカスト会社は、腕のいい金型会社を見つけるのに苦労しており、よい評判を聞くとすぐに引き合いがあるような世情だった。また、自らいろいろな顧客を紹介してくれるダイカスト会社もあった。3カ月後には受注が回復、会社は経営的な危機を脱した。
振り返れば、これは大きな転換点であったに違いない。2016(平成28)年現在でもプラスチック型を製造する会社は業界全体の約3分の1を占めており、競合が多い。これに対し、ダイカスト型製造は1割に満たず、製品単価も高い。
また、複数社との取引の決断も重要なポイントであった。現在でも、メインとなる1社を中心に取引を行なっている会社がほとんどで、取引先の平均数は4〜5社に過ぎない。1社に取引を集中させると、営業サイドも製造サイドともに楽に仕事ができるというメリットがある。半面、相手先の経営状態が悪くなったときのリスクが非常に高くなる。このリスクヘッジとして、できるだけ多くのダイカスト会社と取引をしようという考え方である。
ダイカスト金型への転向と複数社取引への決断。それは、取引先との人間関係に安住せず、常により良いモノづくりに挑み続けることを意味する。80年の危機は、現在のフジイ金型を特徴づける、経営方針転換のきっかけとなった。
NC化へ
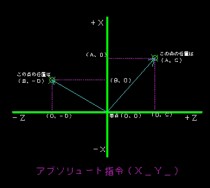
80年代、マシニングなどNC工作機械やワイヤ放電加工機の普及が、金型精度の向上と納期の短縮に大きく寄与した。切削加工工程における技術発展は、この時期一定のレベルに達したといわれる。
特に、NC(Numerical Control =数値制御)による加工技術の登場は画期的であった。これは50年代、アメリカ空軍とマサチューセッツ工科大学(MIT)の共同研究から始まった。「数値制御工作機械において、工作物に対する工具の位置を、それに対応する数値情報で指令する制御方式(JIS)」、つまりドリルなど切削用工具の刃先の動作をコンピュータによる座標軸で指示して行なう加工である。職人による手作業では、技能によって精度や作業時間に大きなばらつきが生じやすく、品質管理が難しい。NC加工によりこの点が克服され、同精度のものを同じ作業時間で、大量に作ることができるようになった。
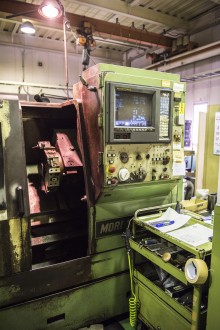
フジイ金型では、1982(昭和57)年には旋盤1台、小型汎用フライス加工機3台、中型フライス加工機2台、研磨機1台、放電加工機1台を有していた。だがその数カ月後の1983(昭和58)年4月、マシニングと放電加工機がそれぞれ加わった。以降、次のように数年ごとに新しいNC切削加工機を購入している。
- 1984年 NCフライス 1台
- 1986年 NCフライス 1台
- 1989年 マシニング 2台
機械を購入する都度、隣に入居していた会社との間にあった仕切り用のベニヤ板を取り払い、作業スペースを拡張しなければならなかった。それでもどんどん手狭になってきたため、社員同士で機械を使用する順番を決め、作業をやりくりしていた。
この時期のNC加工は、今日のような完全自働化の風景とは違っている。当初は工作機械にNCデータを直接入力していた。のちCAM(Computer Aided Machining)の登場により、パソコンでプログラムを作ったのちNC加工機に転送し、加工に使用する刃物やその動かし方を指示できるようになった。ただ転送の際は、データをいったんNCテープに記録(穿孔)し、読み取り専用機械にかけなければならなかったので、NCフライス盤使用時の光景は次のようなものであった。
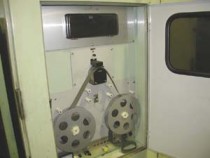
まず、切削用の刃物を付ける。次に、切削データが記録されたNCテープを抱え、読み取り機にヨイショとセッティングする。スイッチを入れる。機械が、テープ上のデータをブァーと読み取る。NC加工機が作動し、終了する。一つの動作が終わると、作業者が刃物をあらたに選別しセッティングし、テープを入れ替える。スイッチを入れる。これを繰り返す。
結局、逐一機械に立ち会わなければならず、今では30分ぐらいで完了する作業に数時間かかっていた。90年代まで続いたこの自動プログラミング(自動プロ)は、文字通り「作業者自身が動くプログラミング」だったのだ。
その後、刃物の自動交換機能を備えたマシニングが、加工の省人化を進めた。ただし、最初に導入したMAZAK-V-10Nでは、指定できる刃物の動作が限られていたため、手作業の部分も多かった。だが数年後の1989(平成元)年に導入した2台では、かなり複雑な動きが可能になっていた。全過程で機械が自ら考えて働く、「自働」の時代に入っていったのである。
アメリカでは、急速にNC工作機械の導入を進めようとした会社側が職人の組合と鋭く対立、NCという形式知と職人的技能である暗黙知を融合させることなく、産業の衰退を招いてしまう。一方、日本の場合、こうした新技術の登場が職人の技能を駆逐することはなかった。ひとつは、零細企業が多かったために、導入がゆっくり進んだことが原因であろう。だが最大の理由は、精度に大きな影響をもたらす、数値化できないカンや手触りを重視し続けたからだと言われている。フジイ金型もその例にもれず、「右手にコンピュータ、左手にヤスリ」で愚直にモノづくりに挑み続けた。
CADの導入
切削加工のNC化の次には、金型業界にもう一つ大きな技術変化が起きた。設計過程の合理化である。CAD(Computer Aided Designing)、つまり、コンピュータの画面上で図面作成を支援するためのシステム(ソフトウエア)が登場した。
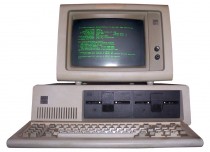
CADはNCの開発に遅れること10年、60年代、やはりアメリカMITの研究による2次元図面のデータ処理システムから生まれた。70年代には実用化され、さまざまな産業分野の設計で応用された。
設計が画面上で行なえるメリットは、効率的であることだ。作図技術を要せず、書き直しも早い。何よりも「分業」ができる。基本的な設計さえしておけば、あとの製図は高度の専門知識やスキルがなくてもできるからだ。さらに、設計パターンの蓄積ができるようになる。ただし、80年代初頭では価格が1台1千万円以上であった。
フジイ金型では1989年頃、2次元CAD を導入した。2次元CADとは、側面、正面、上面などからみた形状の図面を作成するためのシステムである。
それまでは穴開け加工一つをとっても、ドラフターで作成した大まかな図面だけをたよりに、ひとりひとりが穴の大きさや深さ、位置を考えながら作っていった。失敗したら穴を埋めてやり直してそれを完成品にするという具合である。CADは、この「作りながら考える」を「考えながら作る」に大きく変えた。
下表「情報機器の導入年次」によると、90年代までにCADを設置した会社は計8割程度である。
1974年以前 | 1975年 - 79年 | 1980年 - 84年 | 1985年 - 89年 | 1990年以降 | |
---|---|---|---|---|---|
CAD | -- | 3.9% | 15.6% | 58.4% | 22.1% |
CAD/CAM | -- | 1.0% | 6.7% | 42.3% | 50.0% |
NC機器 | 8.4% | 24.5% | 41.7% | 21.1% | 4.4% |
これを見る限り、当社での導入は大勢にならったタイミングだが、周囲には80年代初頭からCADを使用している同業他社も多かったという。機械導入における先進地域だったことがうかがえる。
CAD導入後は、手書きの設計図をパソコンのDOS-Vソフトで置き換える作業が急ピッチで進められた。一時的に、仕事量はずいぶん落ちた。手書きでは3日で仕上げていた図面が、パソコンでは10日かかるほどの手間がかかった。しかし設計主任であった榊間は腹をくくり、システム導入後、ドラフターをすべて捨て、効率化へのレールを敷いた。2カ月後には、元の設計ペースに戻った。
のちにCAD の集約化を行なうため、LAN構築を試みたことがある。その際、1台270万円相当のCAD4台を一挙に購入、費用は700万円だった。フロッピーでデータのやりとりをしていた時代に、無線LANでデータを飛ばす斬新なアイデアだった。しかし、実際には皆同じ部屋で設計をしていたために、データをフロッピーのまま手渡した方が早かった。結局は頓挫してしまったものの、あくまでも効率化をめざすフジイ金型を示すエピソードとして興味深い。
80年代はこのように、職人のカンに頼っていた設計・加工過程のデータ化が、大きく進んだ時期である。だが、製造の主導権はユーザー側ではなく、まだ金型会社側にあったようだ。当社でも、でき上がりが遅いことを心配した顧客が、様子をのぞきにやってきたというエピソードが示すように、納期をはじめ金型会社ペースの時代だった。80年代半ばに一時的な生産の落ち込みはあったものの、平均成長率は10%以上、不況知らずの金型業界と言われていた。
当社でも、人と機械が増え続け、80年代末には社員は20人に達していた。作業スペースは限界に近付き、工具をうっかり取り落としただけで、隣の会社とを間仕切っているベニヤ板の壁を壊してしまったこともある。「がんばって利益をあげて、早く新しい工場に移ろう」と、社員一丸となって朝から晩まで働いていた。
日本全体の経済成長は安定期に入り、80年代の平均伸び率は4%台となっていた。特に1985(昭和60)年、アメリカの対日貿易赤字を是正するための「プラザ合意」以降ドルは急落、1年間でドルの価値は半減する。この出来事は日本の成長基盤を変えた。急激な円高は輸出主体の日本の製造業を直撃、国内工場を海外に移転する企業が相次いだ。いわゆる円高不況である。多くの企業は本業以外に収益を求めた。
こうして日本円は、国内の株式や不動産だけでなく、海外にも投資先を求めて流れ込んでいった。大手不動産会社がニューヨークの摩天楼の象徴、ロックフェラーセンターを買収、1989年末には日経平均株価は史上最高の38,957円44銭を付けた。成長の基盤はモノづくりから金融業にシフトしていた。日本人の多くが産業の空洞化に目をつぶり、「バブル景気」に酔いしれたのである。
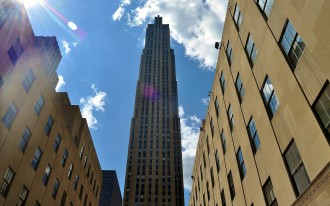