年間300型以上を設計する、20名の技能集団
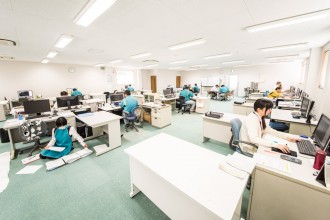
本社工場の一角に設計チームがあります。設計チームには、20名を超えるエンジニアが所属し、金型構想図設計グループ、3Dモデル作成グループ、加工プログラム作成グループの3グループわかれて、年間300型を超えるダイカスト金型を次々と設計しています。
仕様をデータへと変換する
設計業務のスタートは営業からの引き継ぎです。
お客さまと営業で話し合った金型全体や構成部品などについてのニーズ(要求仕様)を、数値に変換し、CAD(Computer Aided Design)で図面としてモニター上に可視化していきます。
主要部品の強度を計算しながら、形状や寸法などの詳細を設計していきます。ダイカスト金型の品質やコストの大半はこの段階で決まるといっても過言ではありません。
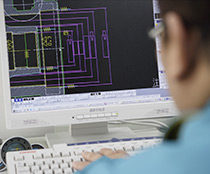
3次元モデリングなどの新技術による設計体制
複雑な形状の金型づくりに不可欠なのが、3D CADによる3次元モデリングです。2D CADでは作成が難しかった曲面なども、リアルに表現できるのが特徴です。
かつては「入社2年目までに、紙の図面を見て頭に金型の形状が浮かぶようになるのがエンジニアへの第一歩」などとも言われていましたが、3D CAD、3次元モデリング技術の進歩により、この鉄則も崩れつつあります。
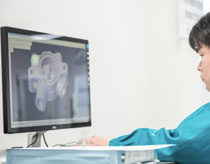
最近では、成形品を3Dプリンターで試作し、問題となりそうな点を洗い出したり、シミュレーションソフトを使った鋳造時の不良予測をするなど、更なる新技術を用いた設計も行われています。
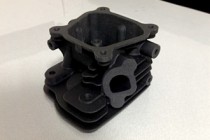
加工プログラム作成
ダイカスト金型は、非常に丈夫な合金を切削することで作り出します。切削作業は自動化されており、マシニングセンタなどのNC(Numerical Control)工作機械がそれを担っています。
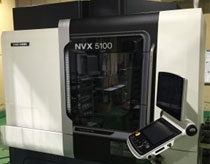
(立形マシニングセンタ NVX5100)
設計では、CAM(Computer Aided Manufacturing)を用いて、これらのNC工作機械に対する加工プログラムを作成していきます。NC工作機械は、機械ごとにそれぞれ向き不向きもあり、それらの能力も加味しながらプログラムする必要があります。
効率の良いプログラムが作れることは、後工程となる製造の業務効率を向上させ、結果的に納期の短縮にもつながります。
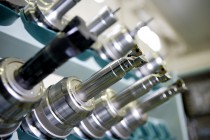
分業と協業
普段の業務では、モニターに向かって作業に没頭する設計チーム。しかし、よりよいモノづくりのためには、部門内外の人たちとの連係プレーも重要です。設計変更などの際には、製造チームを交えたスケジュールの調整を図るなど、担当者同士で打ち合わせをおこないます。
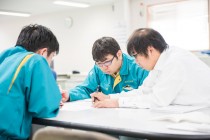